CFD Modeling is Reducing Surprises During Construction
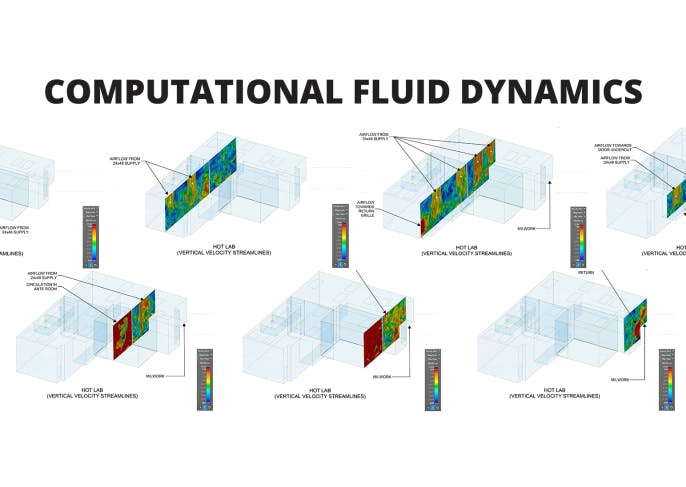
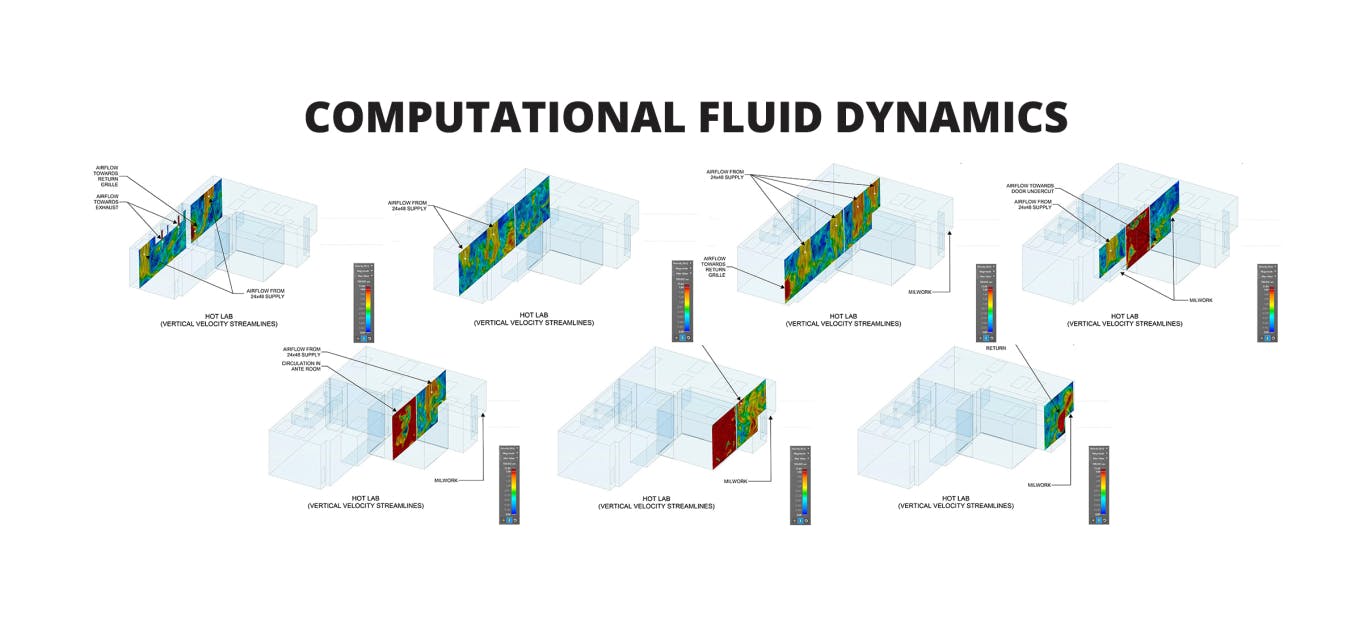
Computational Fluid Dynamics Modeling (CFD) is the art of modeling the air within a space as a fluid and analyzing how different variables such as air flow patterns, velocities, temperatures, and pressures can be affected by a room’s design and internal components. Utilizing both mathematical formulas and principles of physics the design team can model and view a representation of the phenomena related to a rooms’ function.
CFD modeling is a critical pre-construction step used by engineers to compare the results of various facility options during the design phase. The CFD model allows engineers to optimize the space and pinpoint potential problems early which results in time and money savings in the design phase as well as reduced construction costs.
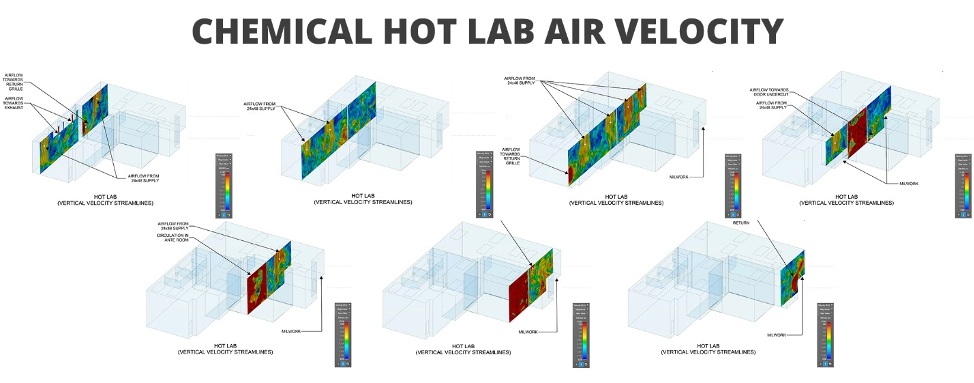
How it Works
Pre-Processing This is the beginning stage where the designers build out the geometry of the space and any associated equipment or obstructions within. Once the basic geometry of the room is modeled the team will start assigning boundary conditions such as flow velocity from a supply grille, supply air temperature, mass flow rates of the return grille(s). As the project progresses and an equipment plan is formed, designers export the equipment out of the building information model and into the CFD model. A heat flow rate associated to the equipment’s equivalent heat load distribution to the space is assigned to the equipment in the model and simulated. Solving Once the information has been set up within the program and the boundaries and internal conditions are set the software can begin to model the conditions assigned in the Pre-Processing stage. The initial conditions will be set and when the simulation starts the team is able to view a visual representation of the air’s fluid dynamical properties. By analyzing values such as velocity, pressure, temperature, and airflow, the team can identify, address and solve design problems that in normal design conditions may be overlooked. Post-Processing Once the results have been returned as values the team can then plot them as scaled color plots, contour plots and various other appropriate representations that can be used to enhance the overall design understanding of the space and advert any negative resolutions that were discovered during the testing process. These can also be shared with the client to detail why certain design changes were needed in a space, especially if the design change may seem odd or nonstandard at the time. Limitations of CFD Modeling Like all models, a CFD model is only as good as the inputs and assumptions used to create the model. It is imperative to hire a qualified, experienced engineer with the knowledge to gather a complete set of data and verify with field measurements where possible. Partnering with a diligent and thorough engineer will ensure the integrity and validity of your model for effective decision making. How Using CFD Modeling Upgrades the Design Process The modeling allows the designers to visually simulate the airflow patterns, temperature and pressure within a space. This enables the team to identify any low-pressure areas, hot spots and areas where the air tends to circulate but not escape and return. Prior to the advent of CFD modeling, engineers and designers often had to make the best assumption that they could with the information present, and using best practices assume the way the air would flow through the space. Now with CFD modeling, the design team can see exactly where the air will go and how to make the design the most efficient without costing the client change orders after the construction has started. For a C1S client, the engineering team was designing a cleanroom. While there are no standards for locating supply and return grilles, it was deemed appropriate to place the grilles on one wall assuming that the air would disperse across the room and circle back to the return grille. After the CFD model was complete, it was discovered that the velocity was high enough to disperse the air across the room, however the model indicated an entrapment of air in the corner of the room caused by the high velocity air which resulted in a lack of return air leaving.
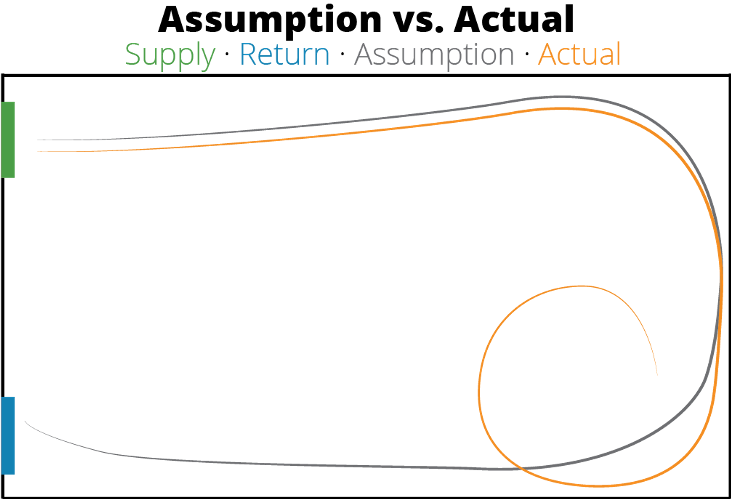
Being able to identify this before the room was being constructed saved the client unnecessary cost increases and delays. The design team was able to simply move the vent to the other side of the room to properly circulate the air.
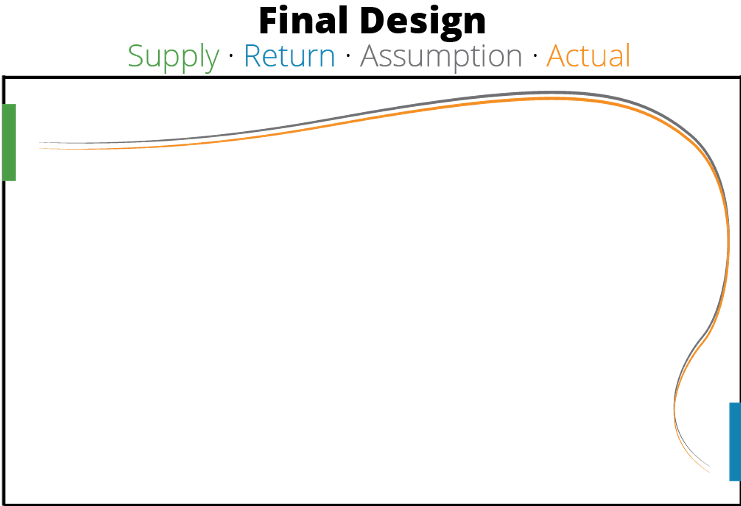

Get the scoop on shut down coordination in manufacturing plants.