Dust Collection in an Industrial Context Promotes Quality, Safety & Health


Enhancing safety, increasing efficiency and reducing costs are important goals to manufacturers. Dust collection systems can play a big role in accomplishing them. In a manufacturing setting, dust can affect the quality of the products produced, impact worker health, and even catch fire or explode.
Dust collection is particularly important to industries such as:
Chemical
Pharmaceutical
Petrochemical
Wood Processing
Food/Agricultural
Paint/Coatings
Often, industries with dust control systems have the responsibility to maintain appropriate particulate concentrations inside and outside a plant. This means that good air filtration and dust-collection systems are essential, along with effective analysis of the operations throughout the plant to ensure proper dust collection is occurring.
Dust collection refers to the removal of solid particles from a flowing air stream in order to provide for the safety and health of employees, eliminate nuisance dust, deliver quality improvements and even to collect powdered products. Dust collectors are the equipment used to separate dust from the airstream and typically contain collection chambers designed to contain low concentrations of particulate, usually below the explosibility limit. Due to the combustibility of many types of particulate, dust collectors are a leading type of equipment to experience explosions, so taking appropriate safety precautions is critical.
Designing a Dust Collection System
The design and implementation of a dust collection system within an industrial context is governed by a variety of codes and standards devised by industry trade groups and governmental bodies, such as the U.S. Occupational Safety and Health Administration (OSHA) and the National Fire Protection Association (NFPA). So, understanding the specific standards and rules applicable to your industry is important. Dust collection system design is a multistage process that involves identifying the area requiring dust collection, the preferred location for equipment, devising the design criteria for electrical and mechanical systems, choosing the appropriate equipment and assessing the explosion risks.
The first step is to identify equipment or areas requiring dust collection and determine the capture device that would work best for each area. The choices include an articulating arm, a direct connection to the equipment or a hood. Consider carefully the location of the dust collection equipment. If it is located in the interior of a building, it should be in a separate room dedicated to dust collection equipment only. Because most building owners don’t want to lose manufacturing space for dust collection equipment, it is highly likely you will have to use an exterior location.
The electrical equipment required for a dust collection system must adhere to specific design criteria. These include controlling static electricity, grounding the equipment and providing vapor and dust-proof light fixtures. Furthermore, depending on the quantity and type of dust, you must decide whether to use “dust ignition-proof” or “dust-tight” equipment. Dust collection also requires special Class II wiring methods designed to protect against the combustibility of the dust, based on whether operating conditions exist that could produce explosive or ignitable mixtures.
Duct Systems for Dust Collection
Designing duct systems for dust collection involves considering capture velocity, sizing and system resistance. The velocity required to capture the dust emissions at the source without compromising the process or product will vary based on the process and the capture device. For example, capture velocity for mixing processes with liquids is below 500 FPM while it’s equal to conveying velocity if connected directly to the equipment.
To appropriately size the ducts, determine the diameter of branch ducts by the size of the factory-installed collar on the equipment or by calculating the equivalent round diameter using the conveying velocity of the dust and the given airflow (CFM). To determine the diameter of the main duct, sketch out the ductwork route, start with the connection farthest from the dust collector and, moving inward, increase the main duct diameter at each duct junction.
Ducts are constructed of either rigid or flexible materials. Rigid ducts are made of plastic, galvanized steel or stainless steel. In industrial applications, metal construction is recommended to reduce the chance of dangerous static electricity buildup. When elbows are required, the ideal maximum is 45 degrees. Flexible ducts are made of rubber or plastic hose and contain a metal grounding helix that MUST be grounded at each end to prohibit static electricity buildup.
To determine the best dust collection equipment to use in a facility, consider the total system CFM, the location of the equipment (whether interior or exterior), whether there is compressed air or a compressor in use, and the type of controls used in the facility. Then, select from the common dust collector system types, which include:
Bag Filters
Cartridge Filters
Cyclone Separators
Electrostatic Precipitators
Preventing Fires & Explosions
Dust collection serves as an important method to prevent fires, as is illustrated in the “Fire Triangle” showing the elements needed for a fire. In our case, dust comprises the “fuel.”
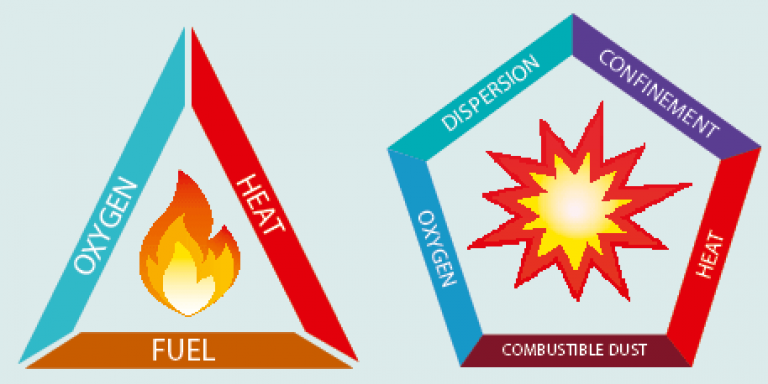
A dust explosion is most likely to occur when a dust cloud is ignited within a confined area. This explosion, however, can further disperse more dust, leading to a second explosion, which can be more dangerous and create more widespread damage than the first.
To help prevent disaster, evaluate the explosion protection options available in light of the explosion risk of the processes occurring in the facility. To do this, know the Kst value of the materials used in the facility. The Kst value indicates the explosive properties of a material measured in the laboratory and is used to quantify the potential severity of a dust explosion. Kst is a relative index, so any material with a value above zero is considered at risk for an explosion. Other than silica and sand, all dust is potentially combustible to some degree. Dust explosion prevention options include a variety of measures that generally fit into three categories: inlet protection, outlet protection and explosion venting.
Kst Values of Common Dusts Any value greater than zero is a potential explosion risk
Tobacco: 12 (Weak Explosion)
Wood Dust: 102 (Weak Explosion)
Rice Starch: 190 (Weak Explosion)
Wood Flour: 205 (Strong Explosion)
Methyl Cellulose: 209 (Strong Explosion)
Barley Grain Dust: 240 (Strong Explosion)
Aluminum Powder: 400 (Very Strong Explosion)
Magnesium: 508 (Very Strong Explosion)
Inlet protection is achieved using one of these methods:
Backdraft damper (most common) – will slam shut by the pressure forces of an explosion, creating a mechanical barrier.
Fast-acting valve – closes within milliseconds of detecting an explosion, creating a mechanical barrier.
Inlet/Outlet Chemical Isolation – reacts within milliseconds of detecting an explosion, creating a chemical barrier that suppresses the explosion within the ducting.
Detect and Suppress – protects the dust collector from ignition sources such as sparks or embers.
Outlet protection methods to prevent dust explosions include:
Outlet Chemical Isolation – reacts within milliseconds of detecting an explosion, creating a chemical barrier that suppresses the explosion within the ducting.
Integrated Safety Monitoring Filter – isolates downstream equipment from the progression of a flame front during an explosion. Allows the recirculation of exhaust air back into the work space when dust is explosive.
High Speed Abort Gates – divert process air and/or smoke to a safe location outside when a possible ignition source is detected entering the system or when a fire is detected.
Explosion Venting is the final method to prevent dust explosions:
Explosion Vents – the vent opens when predetermined pressures are reached inside the dust collector, allowing the overpressure and flame fronts to exit to a safe area.
Flameless Vents – extinguish the flame front exiting the vented area and won’t allow it to exit the device. These vents can be installed indoors and over a standard explosion vent.
Chemical Suppression – reacts within milliseconds of detecting an explosion. It prevents expanding a deflagration by releasing a chemical agent. Used on indoor applications.
Implementing the best dust collection system for your facility will create a safer and healthier environment for your employees, eliminate dust that interferes with producing quality products and prevent hazardous conditions that could lead to an explosion.